What is Porosity in Welding: Recognizing Its Reasons and Enhancing Your Skills
What is Porosity in Welding: Recognizing Its Reasons and Enhancing Your Skills
Blog Article
The Science Behind Porosity: A Comprehensive Guide for Welders and Fabricators
Comprehending the intricate systems behind porosity in welding is essential for welders and fabricators aiming for impressive workmanship. From the make-up of the base products to the details of the welding process itself, a wide variety of variables conspire to either aggravate or alleviate the visibility of porosity.
Comprehending Porosity in Welding
FIRST SENTENCE:
Exam of porosity in welding discloses important understandings into the honesty and quality of the weld joint. Porosity, characterized by the visibility of tooth cavities or gaps within the weld metal, is a typical concern in welding processes. These spaces, if not properly attended to, can endanger the structural stability and mechanical homes of the weld, bring about possible failings in the completed item.

To identify and quantify porosity, non-destructive testing methods such as ultrasonic testing or X-ray evaluation are commonly used. These techniques permit for the identification of internal problems without jeopardizing the stability of the weld. By assessing the dimension, form, and circulation of porosity within a weld, welders can make enlightened choices to boost their welding procedures and attain sounder weld joints.
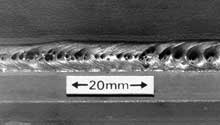
Elements Influencing Porosity Formation
The incident of porosity in welding is influenced by a myriad of elements, ranging from gas shielding efficiency to the ins and outs of welding parameter setups. One crucial factor adding to porosity formation is inadequate gas shielding. When the protecting gas, generally argon or CO2, is not efficiently covering the weld swimming pool, atmospheric gases like oxygen and nitrogen can contaminate the liquified steel, causing porosity. Furthermore, the sanitation of the base materials plays a substantial function. Pollutants such as rust, oil, or dampness can evaporate during welding, creating gas pockets within the weld. Welding parameters, consisting of voltage, present, travel rate, and electrode kind, likewise impact porosity formation. Using inappropriate setups can generate too much spatter or warm input, which consequently can result in porosity. Additionally, the welding technique used, such as gas metal arc welding (GMAW) or shielded steel arc welding (SMAW), can influence porosity development because of variations in heat circulation and gas protection. Comprehending and managing these factors are essential for decreasing porosity in welding operations.
Impacts of Porosity on Weld High Quality
Porosity development considerably endangers the structural stability and mechanical residential or commercial properties of bonded joints. When porosity exists in a weld, it develops spaces original site or dental caries within the material, decreasing the total strength of the joint. These spaces serve as stress and anxiety concentration points, making the weld a lot more at risk to cracking and failure under tons. The visibility of porosity also compromises the weld's resistance to rust, as the entraped air or gases within the gaps can respond with the surrounding environment, resulting in destruction over time. In addition, porosity can prevent the weld's capability to stand up to stress or influence, further threatening the overall quality and reliability of the welded framework. In vital applications such as aerospace, vehicle, or structural buildings, where security and longevity are paramount, the detrimental effects of porosity on weld quality can have severe consequences, stressing the relevance of decreasing porosity via proper welding techniques and procedures.
Methods to Reduce Porosity
In addition, using the suitable welding parameters, such as the right voltage, current, and travel rate, is critical in preventing porosity. Preserving a constant arc length and angle throughout welding additionally aids reduce the possibility of porosity.

Moreover, picking the appropriate shielding gas and preserving appropriate gas flow rates are necessary in decreasing porosity. Making use of the ideal welding strategy, such as back-stepping or using a weaving motion, can also aid disperse warmth equally and lower the opportunities of porosity development. Guaranteeing proper air flow in the welding setting to eliminate any type of potential sources of contamination is vital for attaining Get More Information porosity-free welds. By applying these methods, welders can efficiently minimize porosity and generate high-grade welded joints.
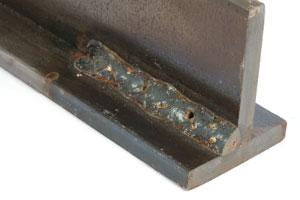
Advanced Solutions for Porosity Control
Applying advanced modern technologies and innovative techniques plays a pivotal function in accomplishing superior control over porosity in welding processes. In addition, employing advanced welding methods such as pulsed MIG welding or changed atmosphere welding can likewise help mitigate porosity concerns.
One more sophisticated service includes the use of advanced welding devices. As an example, using devices with integrated features like waveform control and advanced power sources can boost weld top quality and reduce porosity risks. The execution of automated welding systems click this link with specific control over parameters can considerably reduce porosity problems.
In addition, integrating innovative surveillance and examination modern technologies such as real-time X-ray imaging or automated ultrasonic screening can assist in identifying porosity early in the welding procedure, permitting instant restorative actions. Overall, incorporating these sophisticated options can considerably enhance porosity control and enhance the overall quality of bonded elements.
Final Thought
In conclusion, understanding the scientific research behind porosity in welding is necessary for welders and fabricators to produce top quality welds. By identifying the variables influencing porosity development and carrying out methods to minimize it, welders can enhance the general weld high quality. Advanced solutions for porosity control can better improve the welding process and make certain a strong and reliable weld. It is essential for welders to continuously inform themselves on porosity and execute ideal methods to attain optimal results.
Report this page